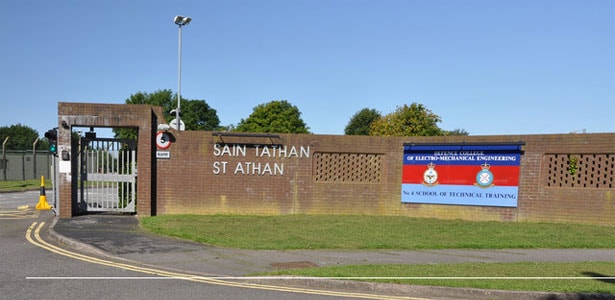
Defence Aviation Repair Agency (DARA) – Aircraft hydraulic ring main systems
Defence Aviation Repair Agency (DARA)
Brief
At the heart of the DARA aircraft facility were two state of the art hydraulic ring main systems that allowed the aircraft hydraulic systems to be fully function tested, filled drain and flushed.
Savery Hydraulics was commissioned to design manufacture and install the complete hydraulic system with the safety of personnel being of paramount importance.
The design needed to;
- Supply a system which met aircraft test requirements, including extremely tight tolerance bands on supply and return pressures as well as flows.
- Supply a system that could automatically meet the dynamic response required to test aircraft which had varying loads and required minimum operator input.
- Minimise the operating and maintenance costs.
- Maximise the system availability and mean
Solution
The ring mains were designed to operate the hydraulic systems incorporated into fast jets that use either self pressurising reservoirs such as the Tornado, Typhoon and Jaguar or fast jets that use pressurised reservoirs such as the Harrier and the Hawk.
Two hydraulic power packs with a total installed power of 1575KW, a total flow of 2520 l/min at a pressure of 315 bar were housed in a purpose built plant room.
The flow was fed through 4” pipe work mains into two hangars which involved an installation of over 3500 metres of pipe work, this fed fluid to sixteen aircraft interface units and allow connection to the aircraft’s systems via flexible hoses.
An electronic/computer system controlled the interface parameters with the aircraft and minimised the human input by:
- The use of a touch screen console adjacent to each aircraft interface unit that allowed programmable pre-set levels to be loaded for various types of aircraft and types of test.
- Matching the flow rates from the power packs automatically via an algorithm to match the actual requirements of the aircraft. This greatly reduced the operating costs and maximised the reliability.
- The inclusion of a PC based SCADA system to provide real time monitoring of the ring main system with historical data being gathered and stored on the flows, pressures, temperatures, operating times and sequences etc., to assist with monitoring and fault finding. This data was displayed and printed in graphical or tabular format.
System contamination monitoring was achieved by using an in-line particle counter. Particle counters were incorporated into the hydraulics system by using a software package called “Modbus”. This protocol enabled the PML2 to be programmed to communicate with a programmable logic controller.
The technicians were able to view the cleanliness of the hydraulic fluid during all periods of servicing and testing ensuring that the correct operating cleanliness was achieved which is critical.
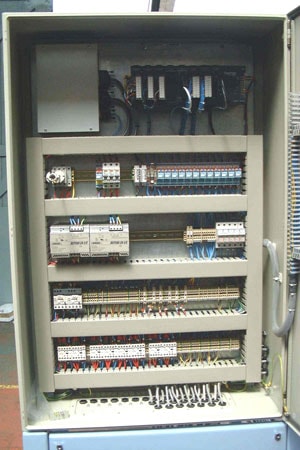